精益制造中的 OEE:目标、评估方法和六大损失
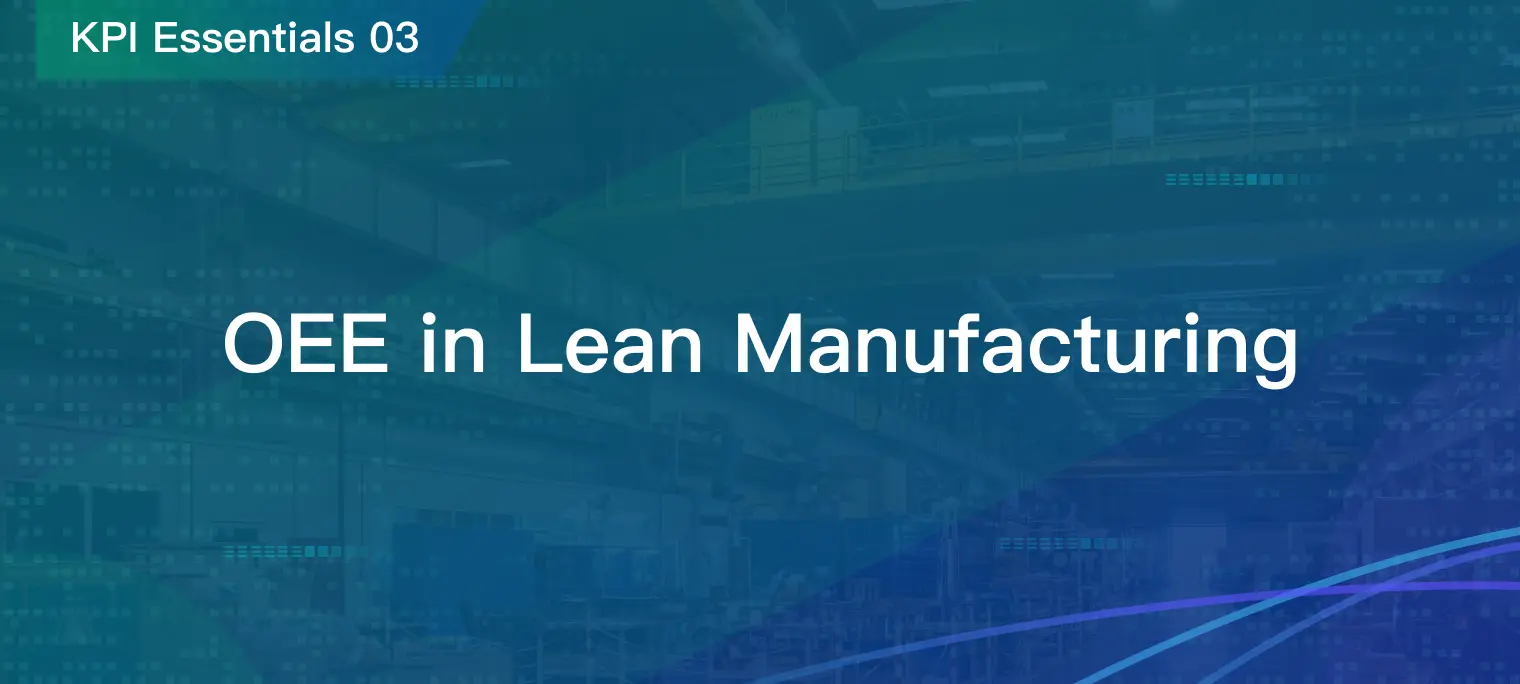
在上一篇文章中我们提到,OEE 是设备综合效率 (Overall Equipment Effectiveness) 的缩写,是精益管理实践的重要组成部分。该指标被制造企业广泛采用,是衡量生产效率的公认标准和基准。OEE 最初由日本设备维修协会开发,是一种用于评估制造设施的技术和组织维度的综合工具。
OEE 的目标
OEE 的核心是全面客观地反映生产环境中生产效率的现状。这使得企业能够深入了解他们的设备和流程运行是否接近其最大潜能。通过综合考虑设备的可用率、性能效率和生产质量等因素,OEE 能够呈现制造过程的总体效率。
OEE 的强大之处在于它能够系统地揭示改进空间。通过分析影响 OEE 的各个因素(包括停机、速度损失和缺陷),可以找出瓶颈、低效和需要改进的地方。这种基于数据的方法让企业能够在流程优化和资源分配方面做出明智的决策。
OEE 还是持续改进的指南针。通过不断地监测和提升 OEE,制造企业可以保障他们的经济绩效持续向好。OEE 不仅能反映当前的生产效率,还有助于制定合理的性能目标,并随着时间的推移评估各种改进措施的效果。
如何计算 OEE
OEE 反映了有效生产时间占计划生产时间的比例。它的计算基于三个因素:可用率、性能和质量。
- 可用率旨在消除中断,保证平稳运行。
- 质量注重完美,目标是减少缺陷产品。
- 性能旨在防止速度下降,保持高效率。
OEE 可以用以下公式计算,其中可用率、性能和质量是制造领域的重要指标。
OEE = 可用率 x 性能 x 质量
可用率
可用率反映了机器实际运行时间占计划运行时间的比例,以百分比表示。计算可用率的方法是,将实际运行时间除以计划运行时间,再乘以 100 得到百分比。
可用率 = 实际运行时间 / 计划运行时间
机器的计划运行时间可以从生产计划中获取。要获得实际运行时间,需要从计划运行时间中扣除所有停机时间。通过分析停机数据,不仅可以揭示停机的原因,还可以发现潜在的改进机会。
性能
要确定性能,需要将实际产量与机器在最高运行速度下有效时间内的最大产量进行比较。
性能 = 实际性能 / 目标性能
实际性能是通过计算包括废品在内的全部产量来确定的。而目标性能则是根据机器每小时的最大产量与实际运行时间相乘来计算的,目标性能反映了在该时间段内的潜在生产能力。
质量
质量是 OEE 必须计算的第三个要素。它是符合质量标准的合格产品在总产品中所占的比例。
质量 = 合格产品 / 总产品
在实际操作中,要计算合格产品的数量,通常是从给定时间段内生产的总产品数量中减去废品和返工产品的数量。这个公式表明,总产品的数量等于合格产品、废品和返工产品的数量之和。
OEE 性能评分
如果可用率、性能和质量没有受到任何影响,就可以实现 100% 的完美 OEE。这意味着在没有中断的情况下,以最高速度生产出全部合格的产品。在实际生产中达到这一理论分数通常不太可能,OEE 分数超过 80% 就可以视为非常出色的表现。大多数制造企业的运营水平通常在 60% 到 80% 的 OEE 范围内。当 OEE 低于 60% 时,意味着工厂存在严重问题,这一水平的分数可以视为警告信号,表明存在巨大的改进空间。
- 80% - 100% 为优秀 - 在实际中难以实现
- 60% - 80% 为良好 - 大部分制造企业的水平
- 60% 或以下为表现不佳 - 有很大的提升空间
六大损失
OEE 的主要目标是减少或消除所谓的六大损失 (Six Big Losses)。它们是造成生产过程中与设备相关的生产效率损失的主要因素。
可用率损失
OEE 的一个基本要素是机器和系统的可用率。正常运行时间是指机器或系统正常运行并进行生产的时间。相反,停机时间是指机器本应运行但却无法运行,从而造成经济损失的时间。
计划内停机
导致机器停机的计划内事件会降低 OEE。这些事件包括更换、维护、检查和清洁等。通过使用专业的软件,可以对这些计划内停机进行细致的分析和优化,以尽量减少它们的影响,尽管它们具有非负面性质,但仍有很大的改进空间。
计划外停机
当计划内的生产因故障、宕机、停电、自然灾害或缺勤等意外事件而中断时,就称为计划外停机。为了减少这些无效时间,需要准确地追踪原因,进行数字化分类和持续分析,以找出流程中的薄弱环节。
性能损失
OEE 的另一个重要要素是机器和系统的性能。这是指在规定的运行时间内,实际生产的产量与理论上能够生产的最大产量的比例。短暂中断或过慢的运行速度都可能导致性能损失。
短暂停
不到一分钟的短暂停是由工具问题、编程错误、传感器拥塞或需要快速清理等原因引起的,通常由操作员解决。这些中断虽然不引人注意,但却会累积数分钟的非生产时间。短暂停是可以预测并能够消除或控制的。
慢周期
当机器因为机龄、维护、故障或材料等因素导致运行速度低于其潜在最高速度时,就会造成损失。与短暂停不同,慢周期情况下生产仍在继续,但以较慢的速度进行。如果无法确定理想的运行时间,管理层可以依据历史数据来确定这些时间,而进行充分研究是确定它们的关键。
质量损失
在 OEE 中,质量损失是指产品质量与预期标准不符。与其他两种损失相比,质量损失的影响要大得多。这是因为缺陷产品不仅浪费了材料,还浪费了生产时间。
即使有缺陷的产品可以修复,返工也要占用操作员和机器资源,因此也属于损失。
生产型废品
有些问题必须进行生产后才能发现,例如过度包装、包装不足、标签错误或包装有缺陷。传感器或摄像头等技术手段可以实时识别质量问题,从而大大缓解这些问题。配合专业的 OEE 软件,这种类型的损失有望在不久的将来消除。
启动型废品
当机器在启动、设置变更或产品调整过程中因不稳定而产生次品时,就会出现这种损失。操作员的专业技能在正确设定和避免反复试错方面至关重要。自动化数字辅助系统可快速显著地减少这种类型的损失。
OEE 的不足之处
随着智能制造领域的不断发展,人们越来越清楚地认识到,仅仅依靠 OEE 可能无法全面反映企业在智能制造方面的成就。对智能制造的评估不应只局限于 OEE,企业应该有更广阔的视野,以鼓励持续的发展和创新。
OEE 的不足主要体现在:
- 缺乏供应链指标 - OEE 虽然可以提高单个机器的效率,但却忽略了制造过程与供应链系统的紧密整合。
- 忽视人力因素 - 技术熟练、积极主动的员工对于完善生产流程和提高生产效率有着重要影响。OEE 并没有涵盖这些因素。
- 忽视环境因素 - 可持续性对制造商来说至关重要,制造商应该考虑其运营对环境的影响。OEE 没有考虑资源利用、能源节约或废弃物减少等方面。
为了有效地分析智能制造计划、评估原材料准备、了解员工技能、以及推动可持续性发展,制造商应该采用更全面的 KPI。
使用 OMH 计算 OEE
EMQ 提出的 Open Manufacturing Hub(OMH)解决方案为制造业的运营带来了 OEE 的显著提升,例如,通过实时监测和数据集成可立即洞察设备性能并进行准确的 OEE 计算。它采用预测性维护算法来防止意外停机,简化报告流程,借助历史数据和分析支持持续改进活动。此外,OMH 还通过优化资源分配、实现远程监测来提高设备的整体效率和生产性能,从而改善 OEE 指标。
结语
总之,OEE 通过对生产效率进行全面评估,在精益管理中发挥着重要的作用。OEE 能够提供客观的洞察、揭示改进的机会、指导决策并支持持续的改进,是提高制造运营整体效率和成功率的基石。在接下来的文章中,我们将探讨为何要采用自动化方法来实施 KPI。