BACnet vs Modbus: A Comprehensive Comparison
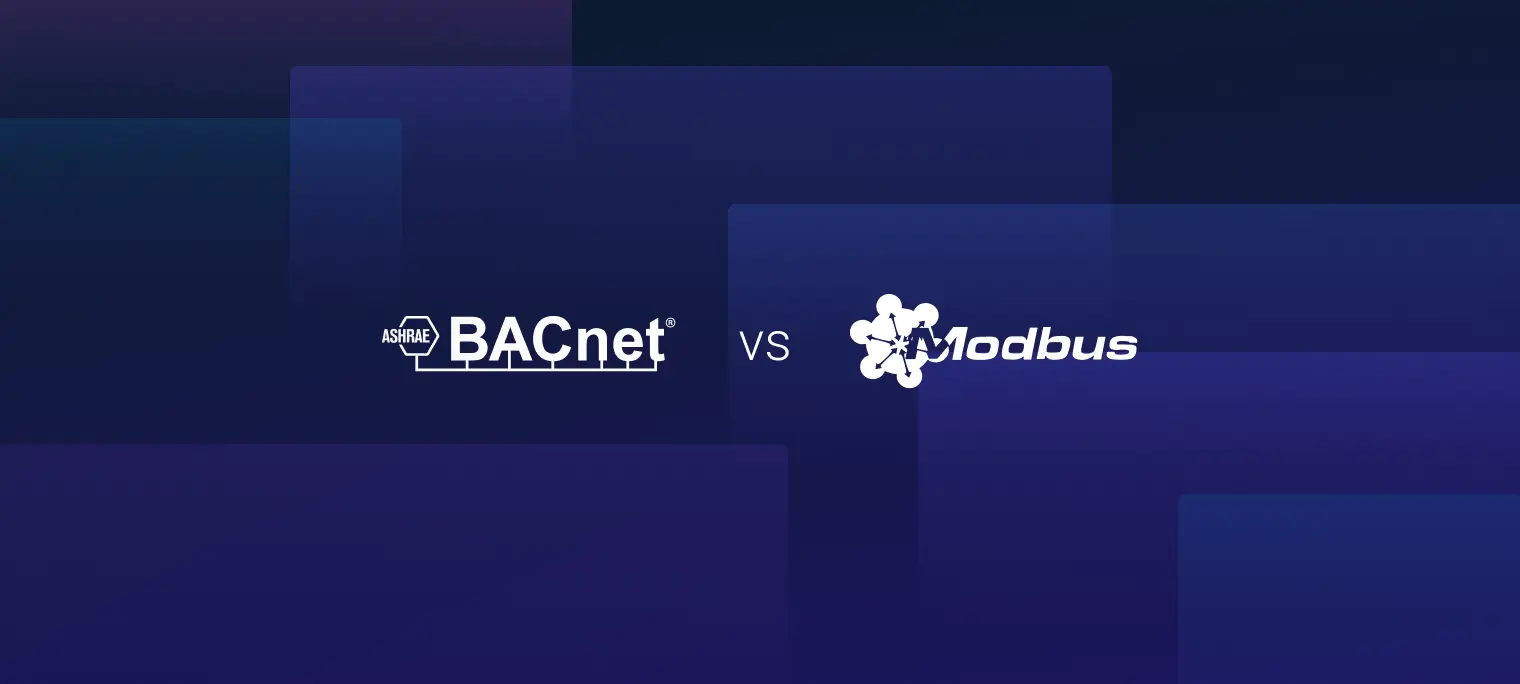
Table of Contents
Introduction
In the field of building automation and industrial control systems, communication protocols play a crucial role in ensuring seamless integration and operation of various devices and systems. BACnet and Modbus are two of the most widely recognized and adopted protocols. These two protocols serve different purposes and each has its unique advantages and limitations. This blog article aims to provide a detailed comparison of these two protocols, highlighting their characteristics, applications, and suitable scenarios. Whether you are an automation engineer, a system integrator, or just curious about these protocols, this comparison will help you understand the advantages and disadvantages of BACnet and Modbus and make informed choices in practical applications.
BACnet Protocol Overview
BACnet, which stands for Building Automation and Control Networks, is a communication protocol specifically designed for building automation and control systems. It is an open standard that ensures interoperability between different devices and systems, enabling them to effectively exchange information and collaborate.
History and Development
BACnet was first introduced in 1995 as a response to the need for a unified communication protocol in the building automation industry. Its openness has contributed to its widespread adoption and continuous development by various professional groups. Since its introduction, BACnet has become an ANSI/ASHRAE standard and is widely used globally.
Main Features
BACnet is characterized by its interoperability, allowing devices from different manufacturers to communicate with each other. It supports a wide range of objects and services, making it highly flexible and adaptable to various applications.
Application Fields
Primarily used in building automation, BACnet facilitates communication between HVAC systems, lighting control, security systems, and other building management functions.
For a detailed introduction to the BACnet protocol, you can read BACnet Protocol: Basic Concepts, Structure, and Object Model Explained.
Modbus Protocol Overview
Modbus is a widely used serial communication protocol in industrial automation environments. Known for its simplicity and robustness, Modbus has become a de facto standard in many industrial settings.
History and Development
Modbus was developed by Modicon (now Schneider Electric) in the late 1970s to meet the need for a simple and cost-effective communication protocol for programmable logic controllers (PLCs).
Main Features
Modbus is renowned for its simplicity, making it easy to implement and maintain. It uses a master/slave architecture, simplifying the communication structure in industrial networks.
Application Fields
Modbus is commonly found in applications such as manufacturing, transportation, and utilities, where it is used to connect PLCs, sensors, and other industrial devices.
For a detailed introduction to the Modbus protocol, you can read Demystifying Modbus Protocols: RTU, TCP, ASCII, and Plus
BACnet vs Modbus: A Side-by-Side Comparison
The table below shows some key differences between BACnet and Modbus at the protocol level:
Feature/Protocol Layer | BACnet (ANSI/ASHRAE Standard 135) | Modbus (Simple, Robust Protocol) |
---|---|---|
Development Time | 1995 | Late 1970s |
Design Purpose | Create an open standard for building automation and control systems | Design a simple and efficient communication protocol for programmable logic controllers (PLCs) |
Standard Setting Organization | ANSI/ASHRAE | Developed by Modicon (now Schneider Electric), now an open standard |
Network Topology | Supports multiple topologies, including star, ring, bus, etc. | Primarily master/slave architecture, but also supports peer-to-peer networks |
Transmission Media | Supports various media such as Ethernet, IP, ARCNET, LonTalk, MSTP, etc. | Commonly used with RS-485 serial links, but also supports Ethernet |
Data Unit | Uses abstract data types (e.g., device objects, properties) | Uses concepts such as registers and coils |
Communication Mechanism | Supports point-to-point and broadcast/multicast communication | Master/slave communication |
Speed and Efficiency | Relatively slower but offers rich functionality and data types | Faster, simplicity leads to efficient data transmission |
Interoperability | Emphasizes interoperability between devices from different manufacturers | Widely supported, but may require additional configuration for interoperability |
Security | Provides security features such as authentication and encryption | Basic protocol does not include security features |
Application Fields | Primarily used in building automation, such as HVAC, lighting, security systems, etc. | Widely used in industrial automation, such as PLCs, sensors, etc. |
Configuration Complexity | Configuration can be complex, requiring deep understanding of the protocol | Configuration is simple, easy to implement and maintain |
Scalability | Good scalability, supports large and complex systems | Suitable for small to medium-sized systems, simplicity limits scalability in large systems |
International recognition | Internationally recognized as the standard in the global field of building automation | Widely recognized internationally, especially in the field of industrial automation |
Actual Use Cases
To illustrate the practical impact of choosing one protocol over another, let's consider a few case studies:
Building Automation
In a large commercial building, BACnet was chosen because it could integrate various systems such as HVAC, lighting, and security. The result was the establishment of a highly interoperable and efficient building management system.
Manufacturing Plant
A manufacturing plant chose Modbus because of its simplicity and the need for fast, reliable communication between PLCs and sensors. The plant benefited from the low cost and simple maintenance of the Modbus system.
Smart Factory
The BACnet and Modbus protocols are not exclusive and can be used in conjunction in some scenarios. In the scenario of building an Internet of Things platform for a smart factory, BACnet may be used for status monitoring and control of HVAC, lighting, and security systems. Modbus can be used for status monitoring and action control of production equipment.
Selection Guide
When deciding whether to use BACnet or Modbus, consider the following factors:
- Cost: Modbus may be more cost-effective due to its simplicity.
- Complexity: BACnet offers more features but may be more difficult to implement.
- Scalability: BACnet's flexibility may make it more suitable for larger, more complex systems.
- Specific Requirements: Consider the specific needs of your application, such as the types of devices involved and the required communication speed.
NeuronEX: An Industrial Gateway Supporting Both BACnet and Modbus Protocols
NeuronEX is software tailored for the industrial sector, focusing on equipment data collection and edge intelligent analysis. It is primarily deployed in industrial settings, facilitating industrial equipment communication, industrial bus protocol acquisition, industrial system data integration, edge-level data filtering and analysis, AI algorithm integration, and integration with IIoT platforms. NeuronEX provides multi-protocol access capability, supporting simultaneous access to dozens of industrial protocols such as Modbus, OPC UA, Ethernet/IP, BACnet, Siemens, Mitsubishi, and more.
The NeuronEX BACnet plugin can act as a client to access BACnet devices. For more information, you can read BACnet/IP | NeuronEX Docs and Bridging BACnet Data to MQTT: A Solution to Better Implementing Intelligent Building.
The NeuronEX Modbus plugin can act as a master to access slave devices. For more information, you can read Modbus RTU | NeuronEX Docs and Bridging Modbus Data to MQTT for IIoT: A Step-by-Step Tutorial.
Conclusion
BACnet and Modbus are both powerful protocols with their own strengths and weaknesses. BACnet excels in building automation because of its interoperability and rich features, while Modbus is very suitable for industrial applications that require simple, reliable communication. Understanding the differences between these two protocols is crucial for choosing the right protocol for your project, ensuring effective system integration and performance.