Measuring Excellence: A Deep Dive into KPIs for Smart Manufacturing
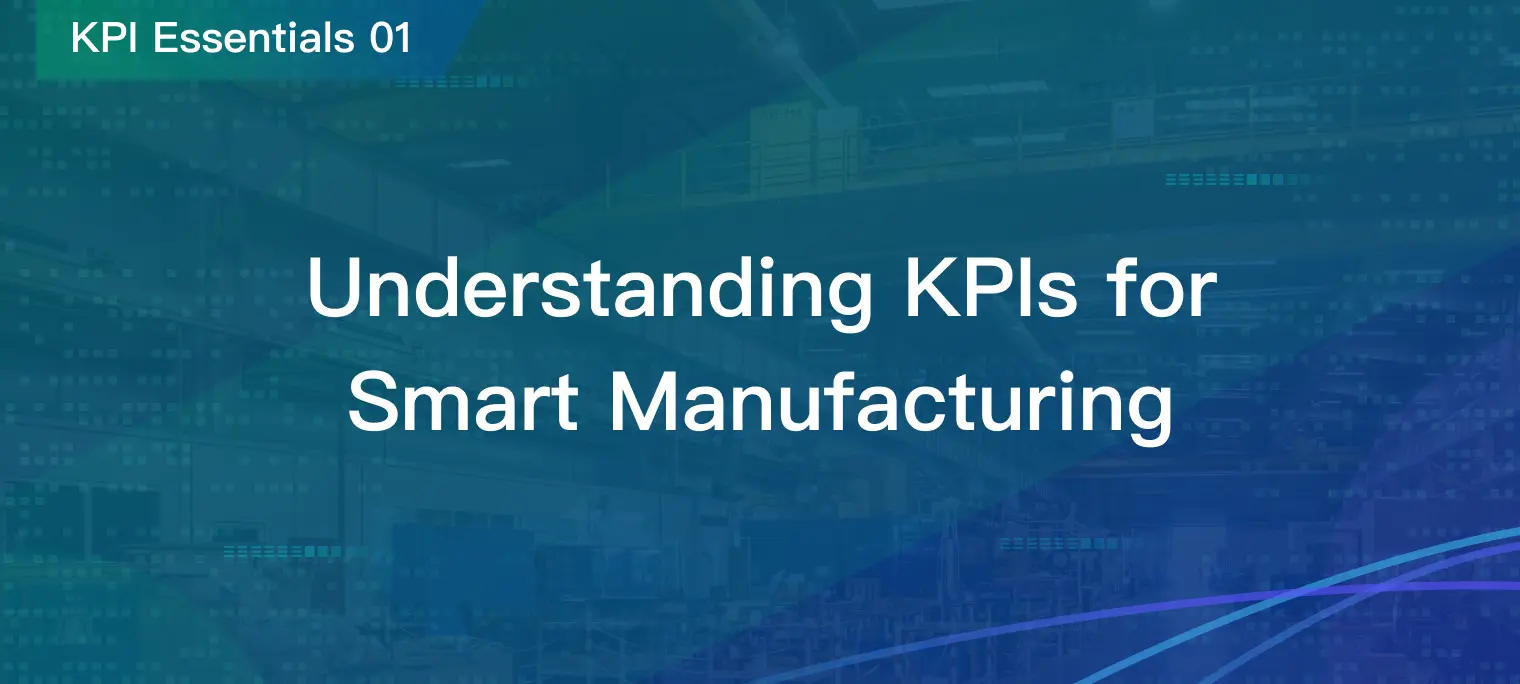
Table of Contents
- What is the Manufacturing KPI?
- What is the Difference Between KPIs and Metrics?
- What Are the Advantages of Using Manufacturing KPIs?
- What is the Vital KPI for Production?
- What Makes a Good Manufacturing KPI?
- What Are the Lean Manufacturing KPIs?
- How to Make the KPIs Actionable
- Easily Track Your KPIs with OMH
- Conclusion
The pursuit of expanding a business's top line, aiming to capture a larger market share for greater profits, is a common goal. Therefore, the presence of indices or figures to measure performance is essential. This is precisely where Key Performance Indicators (KPIs) tailored to the manufacturing sector become instrumental. This series of blogs aims to provide you with a straightforward comprehension of what KPIs are and how they are employed in the manufacturing context. And we will start from the fundamental concepts of KPIs in the first episode.
What is the Manufacturing KPI?
A manufacturing Key Performance Indicator (KPI) or metric is a precise, measurable gauge utilized by the manufacturing industry to assess its performance across time. Manufacturing firms employ KPIs to observe, evaluate, and optimize operations, often benchmarking their efficiencies against those of their counterparts in the same sector.
What is the Difference Between KPIs and Metrics?
KPIs serve as instruments for tracking crucial measurements, aiding businesses in making pivotal choices. KPIs should align with business objectives and provide insights into achieving these objectives.
Metrics encompass a broader category, while KPIs represent a subset of these metrics. Metrics quantify the business's performance in specific domains, while KPIs are those metrics deemed most indispensable for the business's success. While companies frequently monitor standard KPIs like Revenue Growth and Profit Margins, key performance indicators tailored to production play a pivotal role in optimizing that facet of operations.
What Are the Advantages of Using Manufacturing KPIs?
By reviewing KPIs regularly, manufacturers can check on how they are measuring up with important metrics and have the following benefits.
- Performance Monitoring: KPIs provide real-time insights into the performance of various manufacturing processes, helping identify deviations from the desired standards.
- Continuous Improvement: By tracking KPIs, manufacturing companies can identify areas for improvement and implement strategies to optimize processes, reduce waste, and enhance efficiency.
- Data-Driven Decisions: KPIs enable data-driven decision-making. Manufacturers can make informed choices based on quantifiable metrics rather than relying on guesswork.
- Goal Alignment: KPIs help align the efforts of different teams and departments toward common goals and objectives.
- Benchmarking: Manufacturing companies can compare their KPIs against industry benchmarks to understand their competitive position and set realistic performance targets.
- Resource Allocation: KPIs help allocate resources effectively, ensuring that investments are directed toward areas that require improvement the most.
What is the Vital KPI for Production?
KPIs related to quality control and operational efficiency are essential because they provide measurable insight into how well these critical functions are being performed. By monitoring KPIs related to factors such as defect rates, product consistency, production cycle times, and process compliance, companies can identify areas for improvement, implement corrective actions, and optimize their processes.
One of the most important KPIs is Overall Equipment Effectiveness (OEE), which is one of the top five KPIs in manufacturing across industries and global regions. Improving operational efficiency is a top priority for survey respondents, serving as a key measure of the success of their intelligent factory initiatives.
Notes: Part 3 will discuss OEE in details
What Makes a Good Manufacturing KPI?
Numerous manufacturing KPIs are widely accepted as industry standards. However, it's important to recognize that not all of them are universally applicable to every manufacturer. While many can be relevant, others may not align with the company’s goal. In certain cases, a conventional manufacturing metric might not even exist for the specific aspect you wish to measure. If you're planning to devise your own production metric, several factors should be considered.
- Alignment with Company Goals: All companies have objectives they are striving towards. KPIs should align with your company’s goals to help measure your success towards those goals. Every KPI needs a clearly defined goal.
- Clarity and Measurability: Each KPI must define and measure something tangible to achieve the goals. KPIs should be as specific as possible to be useful. There must be a clearly defined data source with a strict procedure for how the data is measured or collected.
- Attainable Value: A KPI is an attainable value and must be actionable, meaning that the data it provides is actively used to make necessary improvements when needed.
- Real-time Reporting Dashboard: Using centralized data along with real-time manufacturing dashboards can immediately generate reports on performance, as well as send alerts when a KPI starts to underperform.
What Are the Lean Manufacturing KPIs?
Lean manufacturing, which originated in Japan (specifically associated with Toyota), is a practice in which companies strive to reduce "waste" while maintaining productivity. In this context, "waste" doesn't refer to physical garbage or production waste. Instead, it encompasses any activity that doesn't add value from a customer's perspective view. Overall equipment effectiveness, production schedule attainment, total cycle time, and scrap are some examples of lean manufacturing KPIs. Another benefit is that it also evaluates the progress of lean process improvement initiatives.
How to Make the KPIs Actionable
Measuring something is of little value unless you intend to act on the insights you gain. It's critical to prioritize KPIs that directly contribute to the growth of your business and use them to drive tangible improvements.
To maximize the effectiveness of KPIs, it's important to share measurements with key stakeholders. The input and feedback you receive from these stakeholders will serve as a valuable resource for refining and improving your chosen KPIs. These indicators should serve as a lens that highlights both areas of strength and potential for improvement, facilitating informed adjustments.
When KPIs are aligned with your business goals, they become catalysts for actionable steps that set your course for positive results. While the range of manufacturing KPIs is diverse, these commonly used KPIs provide a solid foundation. However, each company must develop KPIs that align with its unique strategic goals.
Easily Track Your KPIs with OMH
As a manufacturing business expands, the organization should have a powerful tool to capture and keep track of KPIs. The Open Manufacturing Hub (OMH) solution presented by EMQ provides the automation and modules to operate efficiently. It provides dashboards that show real-time metrics and KPIs to gain business insight. A modern IIoT solution has advanced capabilities that allow you to identify and capitalize on opportunities to increase productivity and revenue.
By seamlessly integrating information technology (IT) and operational technology (OT), OMH gains the ability to effectively gather data from various devices and systems within the manufacturing environment. These devices might include specialized machinery, sensors, production lines, and other components critical to making those KPIs. These devices operate in disparate communication protocols, making data capture complex. OMH overcomes this hurdle through its powerful connectivity features. It establishes connections with a wide array of devices, regardless of their underlying technology or communication methods. This enables the solution to aggregate data from sources that were previously difficult to access and integrate.
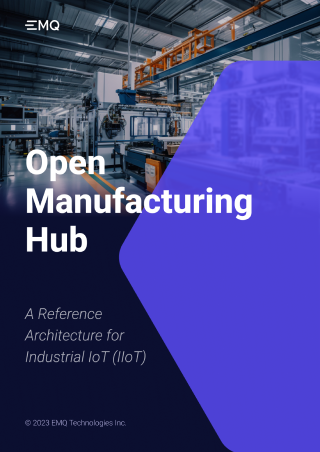
Conclusion
KPIs are invaluable tools for guiding important business decisions. Those who use KPIs must take ownership of the specific manufacturing metrics relevant to their roles and monitor them consistently to facilitate necessary improvements. Adaptability is critical for KPIs, with the ability to evolve based on prevailing circumstances; this flexibility ensures effective monitoring of specific situations.
KPIs retain their power by focusing exclusively on key management concerns. By focusing on critical issues, these indicators maintain their relevance and effectiveness, contributing to informed decision-making. To strike the right balance between comprehensiveness and manageability, it's best to keep the number of KPIs to a manageable number around 10. This selectivity prevents overwhelming complexity, which could dilute the attention given to each metric and make it less impactful. In Part 2, we will give out recommended 10 KPIs that are usually used in manufacturing.